Labeling expenses don’t account for even 10% of operational costs, but nevertheless, they are essential to your supply chain. While seemingly unimportant, your labels can dictate whether or not your products make it past the loading dock since they carry crucial information such as delivery addresses, compliance standards, safety instruction, identification, and more. By choosing poorly made cheap labels, you run the risk of setting up operations for disaster.
Simply put, operations screech to a halt without labels. If labels peel easily or smudge under heat or abrasion, crucial asset information is lost creating delays, bottlenecks, and out-of-stocks. All of these can lead to heavy fines, missed delivery dates, and loss of revenue. To prevent these issues, we recommend assessing your labeling operations.
How do I know my label is poorly made?
Poorly made labels often show tale-tell signs before application. Because they are not made with quality materials, nor are they tested before application, inferior labels tend to:
- Leave behind residual fiber pileup, which clogs printers and distorts information.
- Overwork or distort printheads, leading to premature printhead failure.
- Leak adhesive from inconsistently manufactured rolls.
- Fade under extreme temperatures and humidity.
If your labels present any of these signs and more, then it is time to switch to a better alternative.
How do I spot a good label?
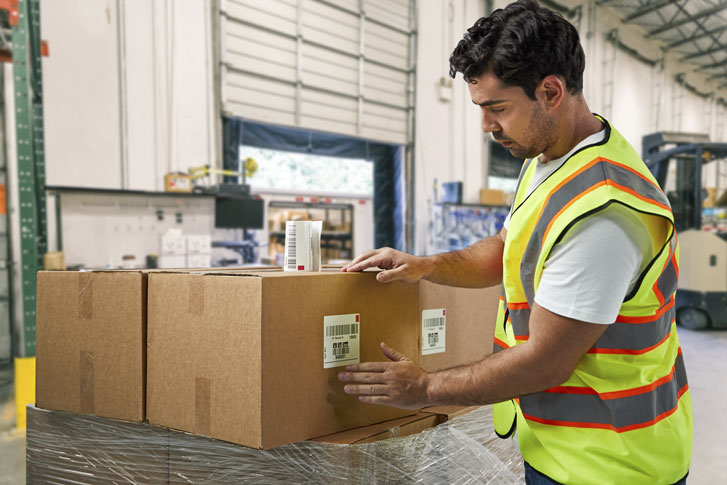
Zebra Quality Labels Are Designed for Your Warehouse
Quality labels such as Zebra’s Certified Consumables should be made from quality materials that withstand both application and storage environments. Moreover, proper labels should be certified to meet compliance standards of whichever industry they will serve; otherwise, your inventory runs the risk of being sent back to the warehouse. Lastly, quality labels maximize your printer lifespan, reducing bottlenecks, printer downtime, and frequent IT visits.
Can I just buy the most popular label to resolve printing issues?
There is no one-size-fits-all labeling solution because the application and budget requirements vary greatly from business to business. There are also different compliance standards certain kinds of products (like food for example) need to follow. Non-compliant labels can prevent or delay your product from reaching the consumer, forcing them to look elsewhere. For example, suppliers can pay fines up to $500 per late order or more from major retailers. Fortunately, Avalon offers Quality Compliany Zebra labels of all types, which gives you the ability to customize label composition, size, color, and many other factors to create a system that fits into your workflow.
Where can I find better labeling alternatives?
As a Zebra Premier Solutions Partner, we work with a wide variety of labeling solutions. Plus, with Zebra labels, you can work with us to create a cost-effective labeling system with both quality consumables, durable printers, and enterprise-grade scanners.
To start your labeling assessment, reach out to Raymond Scipioni and maximize your label’s efficiency with our vast portfolio of quality consumables, designed to meet your application requirements while exceeding your expectations.