Most business operations use labels at some point. At the very least, labels are used for shipping, product or asset identification, work on process tracking, item location, warning notices, and the list goes on…
While everyone wants to save money, many operations overlook the cost of labels or the cost of not labeling correctly.
Label technology has changed as much as anything else in our high-tech world. Improvements in adhesives, top-coating, methods of dispensing and applying, and the label materials themselves had undergone myriad changes – many of which are not known to the average manager.
Why ask about labels?
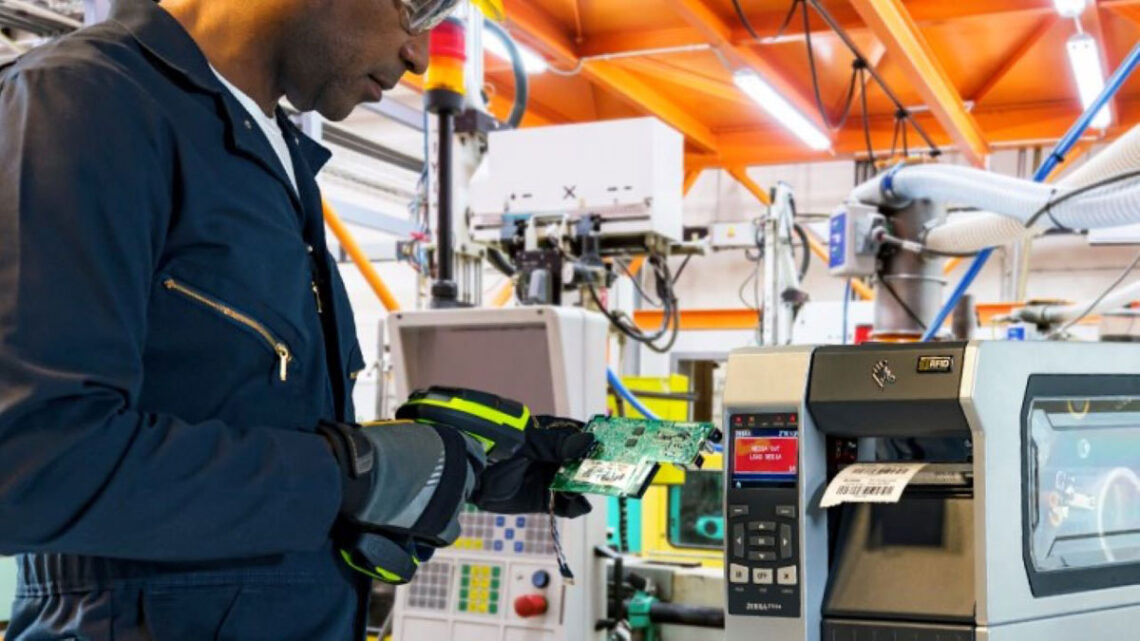
Why Ask about Labels for Hidden Improvement
Avalon has found many “hidden” opportunities for customers to extract cost savings from labeling operations. Simple ways to reconfigure label formats or packaging can result in significant operational savings. Moving from a more optimal form of printing technology can reduce material costs and improve environmental or “green” operation. Logistics programs to leverage production economies of scale are often underused as are savings in overall printer support.
When to ask about labels?
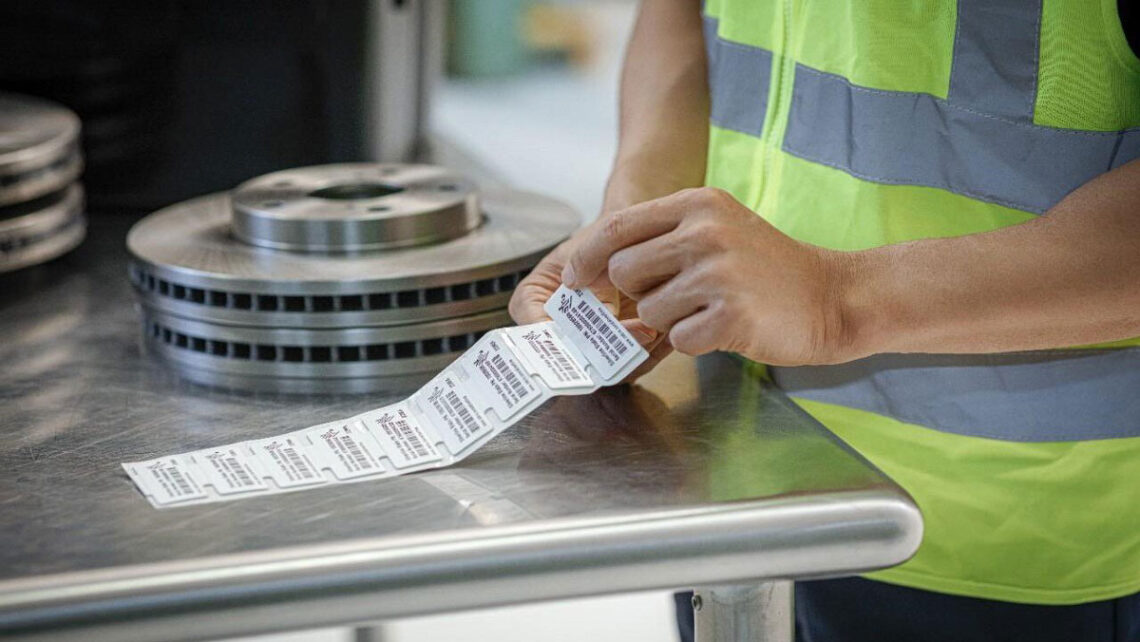
When to Ask About Labels for Hidden Improvement
Label cost is not considered a major expenditure by companies concentrating on the three P’s – People, Plant, and Product. Since potential savings can be overlooked in an assessment. An educated label specialist often produces significant savings. If you think your labeling operations are optimized, it is still time to ask about labels. “Hidden” savings in label costs cannot hide from a label professional. If you think your labeling operations may not be optimized or it has been a long time since anyone took a good hard look, then, chances are, you may be able to save more than you thought possible.
Who to ask about labels?
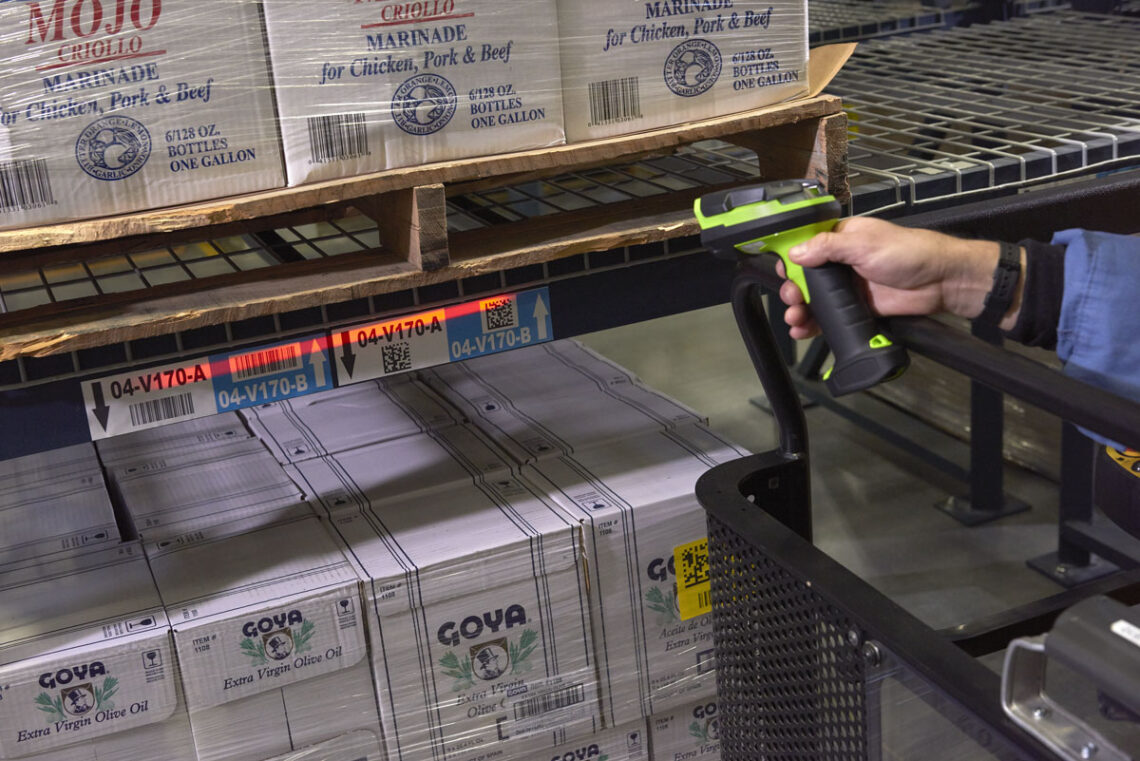
Who to Ask About Labels for Hidden Improvement
A label manufacturer knows about labels. However they may not specialize in printer technology, business operations, and logistics, and associated data collection technology – they are all interrelated. Avalon can not only look at the “label” itself but also all components of your operations before and after the label is applied.
There is a good chance that your labeling system can benefit from an optimized solution. To explore your options, contact our labeling expert, Raymond Scipioni, for an in-depth assessment of your current system.